

It’s always better to start off with conservative settings and slowly increase them until you find the limits of your machine. Sorry I got grumpy but its been a bad day. If you don’t trust my advice then don’t use Ok. I have built over 40 machines, including half a dozen WorkBee 1000x1000’s. Spend the money and buy an Ethernet Smooth Stepper or something similar if you want the best performance.
#Novusun nvcm 6v2.1 software
I’ve never trusted cheap Chinese controllers because they have poor software and poor hardware design and refuse to fix bugs. If it doesn’t meet your expectations, get better hardware. If you combine high microstepping rates, small motors, and fast acceleration it is a recipe for lost steps. Also, torque drops off with higher microstepping numbers as well. The motor has only a fraction of the torque at higher RPM’s than it does at at stop. Stepper motor torque curves drop off almost linearly with speed. If you try to accelerate the system beyond the capability of the motors, it will lose steps. 500 mm/sec^2 would not be attainable even with 365 oz/in motors. If you try to accelerate too fast, the motors won’t have enough torque, and it will lose steps. You need to overcome the static and dynamic inertia of the system. Google “NVUM controller and Mach3” to see if there are others with problems like yours.Īcceleration and fast movement are two completely different things. There may be some settings in Mach3 General Config or Plugin Config screens that you have to tweek.
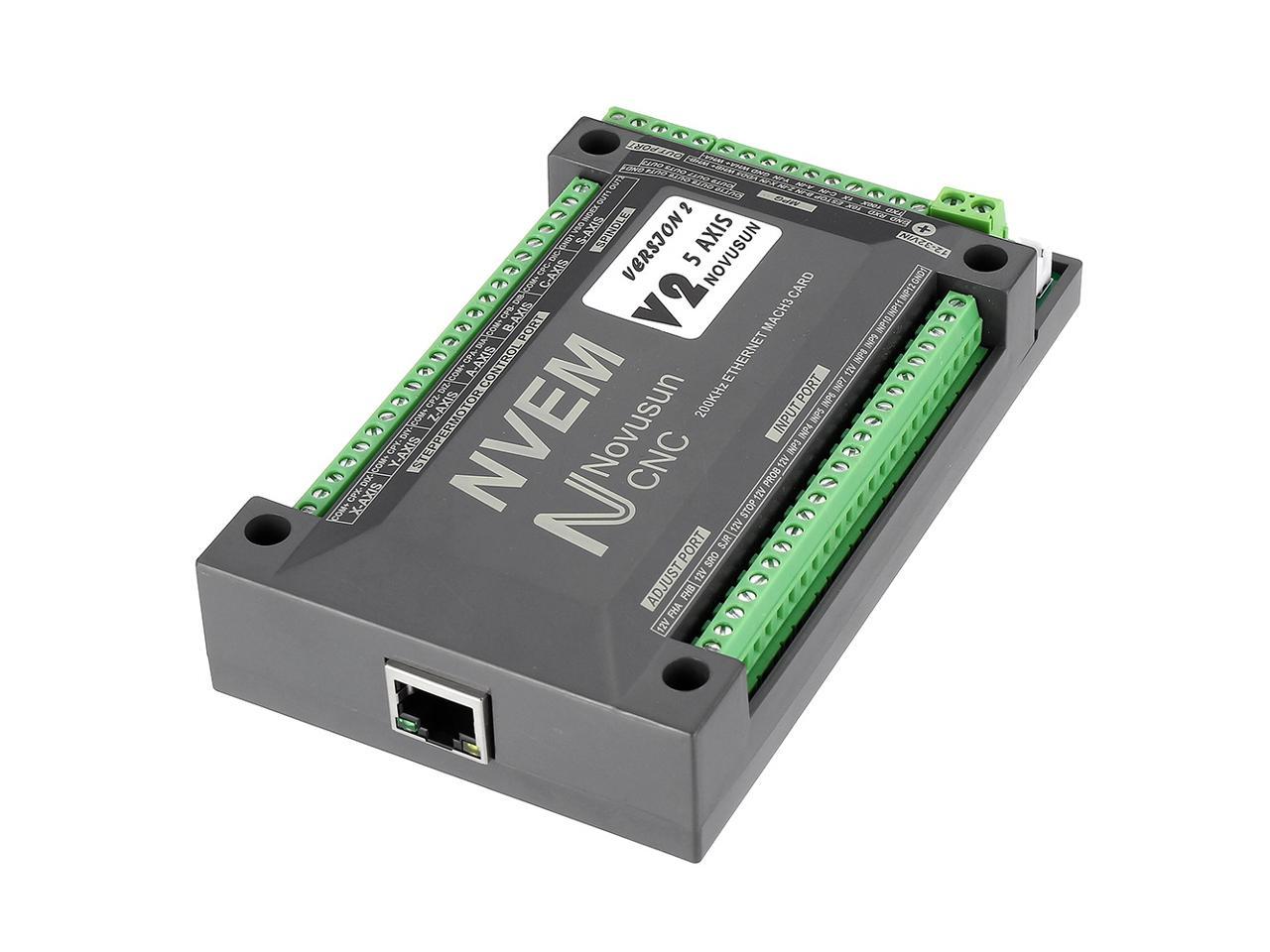
Your computer has lots of RAM and sounds like a fairly fast machine, so that’s not likely it. No surfing the web or recalculating spreadsheets while Mach3 is running. Make sure nothing else is running but Mach3.
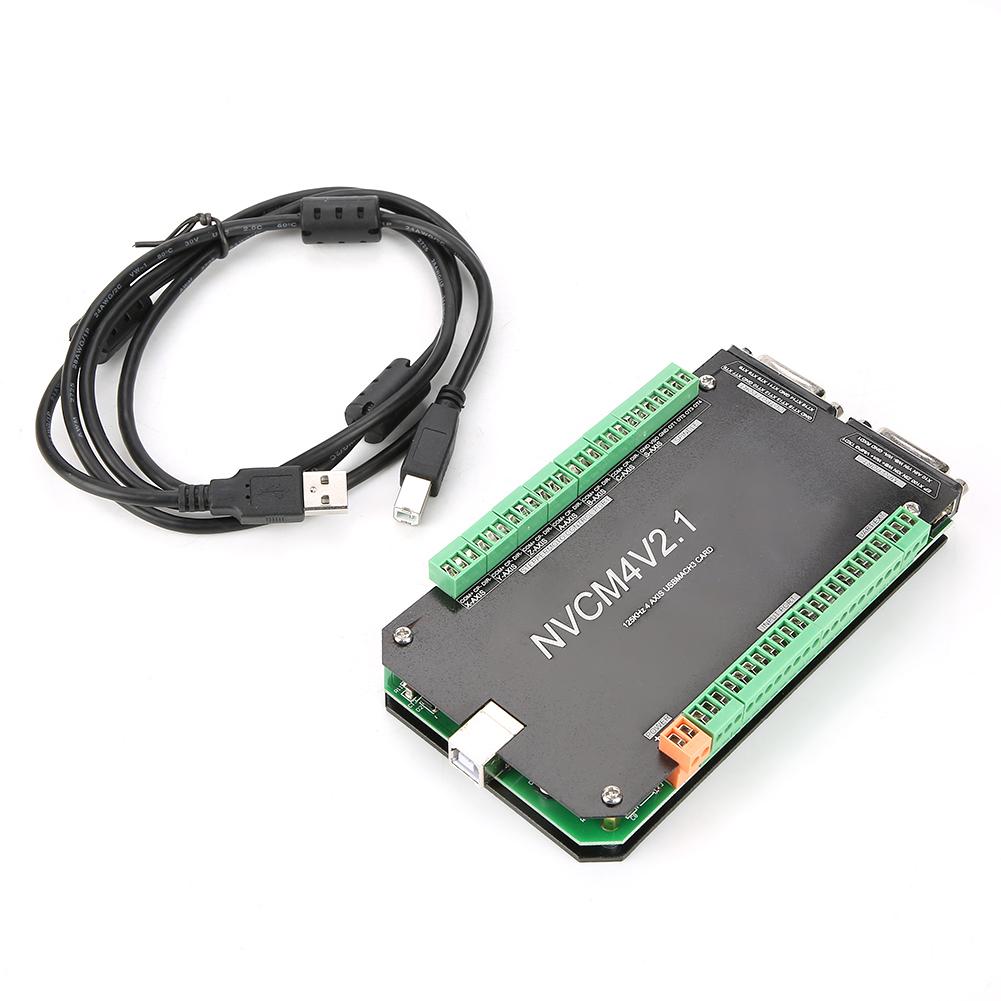
Try a different port.Īlso, Mach 3 is famous for hiccuping if you are running other applications at the same time. Check to see that your USB port is not damaged, laptops seem prone to baked USB ports. As I said before, use the shortest USB cable you can, keep it away from power cords, and make sure it has the ferrite “Lumps” on it.
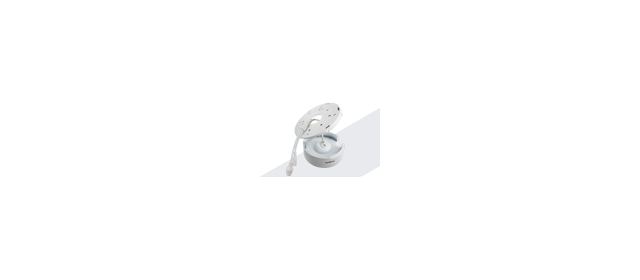
If it loses connection, it would cause it to stop executing. From your description, it may be something to do with the USB connection. It’s just executing the g-code sent to it. The router doesn’t know the difference between a 2D and a 3D cut. You may need to increase the pulse width on the motor pulse output, I don’t know what the specification is for the NVUM, but if the pulse width is too short, it may miss some. What is the motor maximum speed? Here I wouldn’t use more than 3000-3500mm/min with standard 1.2N/M motors. Make sure your USB cable is as short as possible, and has ferrite “lumps” on it to reduce noise.ĭon’t plug the router into the same outlet as the machine power supply and What do you have your motor acceleration set to? I would suggest no more than 50 or 60 mm/sec^2. Check the locking collars on the leadscrews to make sure they are tight and not allowing end play on the screw. If you can’t turn them by hand, or they are very tight, back off the adjusters a bit. Wheels should be tight, but you should still be able to turn them manually with your fingers.
#Novusun nvcm 6v2.1 free
You should not feel any “clicking” or free play in any axis. Circles should be round and same radius all around, squares should be square and same width as height.Ĭheck to make sure all axes have zero play by grabbing the carriage and trying to move it side to side, forward and back, and up and down.
#Novusun nvcm 6v2.1 driver
Check the motor and driver wiring to make sure you don’t have a loose connection on the motor leads or one of the driver inputs.ĭo a simple g-code program with just a few circles and squares, run it, and measure them for size. I wouldn’t use 1/16 unless you have high torque motors. I also think you should use maximum 1/8 microstepping. I wouldn’t recommend taking driver power from the controller, because you could be drawing almost 12A if all 4 motors are running at once, who knows how thick the traces on the controller board are? Do not daisy chain driver power together, run separate wires to the supply for each driver. You should have each stepper driver power input wired directly to the power supply thru 5A fuses.
